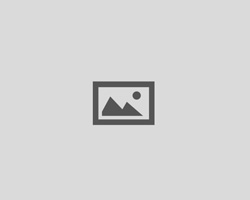
Objective: Design a hand-held medical laser system from concept to final assembly test.
Solution: Create models at every stage using the SD300 printer where the customer can evaluate ergonomic design, final concept and functional testing.
A leading international product design and engineering firm, Nekuda DM, used the SD300 at every stage of design while working on a hand-held medical laser project for their customer. Starting with conceptual sketches, solid 3D parts were built for design and ergonomic evaluation. Utilizing the look and feel of the solid models from the SD300, the customer was then able to adjust the design concept and shape of the device.
The device was then broken down into parts, separate pieces were constructed with snaps, holes, pins and ribs according to the internal technology and each was printed using the SD300 for form, fit and functional testing. A final assembly of the product was printed as well to verify accuracy. In all, over 12 models were created during the project using the SD300 allowing the customer to be a part of the process at each phase.
Using the SD300 every step of the way, Nekuda reduced the design process on this project by weeks, saving their customer valuable time and money. Your company can benefit as well from the many ways to use the SD300.